Dragon Quartz proudly stands as a leading provider of Quartz Fabrication services, offering high-quality quartz products that meet international standards and satisfy the diverse needs of clients around the world. Backed by a team of experts and state-of-the-art technology, Dragon Quartz delivers excellence in every product, ensuring both durability and aesthetic appeal. In this article, we will explore the quartz fabrication process at Dragon Quartz, the strict quality standards we follow, and the reasons why Dragon Quartz is the ideal partner for modern interior projects.
1. Overview of Quartz Fabrication
Quartz Fabrication involves cutting, shaping, and finishing quartz slabs to create final products such as countertops, vanities, wall panels, and flooring. This process requires a high level of precision, blending advanced technology with expert craftsmanship. Dragon Quartz has distinguished itself in this field by producing top-quality products that meet international standards while providing maximum customer satisfaction for projects of all sizes.
More about Dragon Quartz’s Quartz Fabrication
Dragon Quartz – A Pioneer in Quartz Fabrication
As a leader in quartz fabrication, Dragon Quartz excels thanks to its modern production processes and experienced team. We are committed to meeting the highest industry standards, from sourcing raw materials to completing the final product. Every piece crafted by Dragon Quartz is a testament to exceptional craftsmanship, durability, and aesthetic refinement.
2. The Quartz Fabrication Process at Dragon Quartz
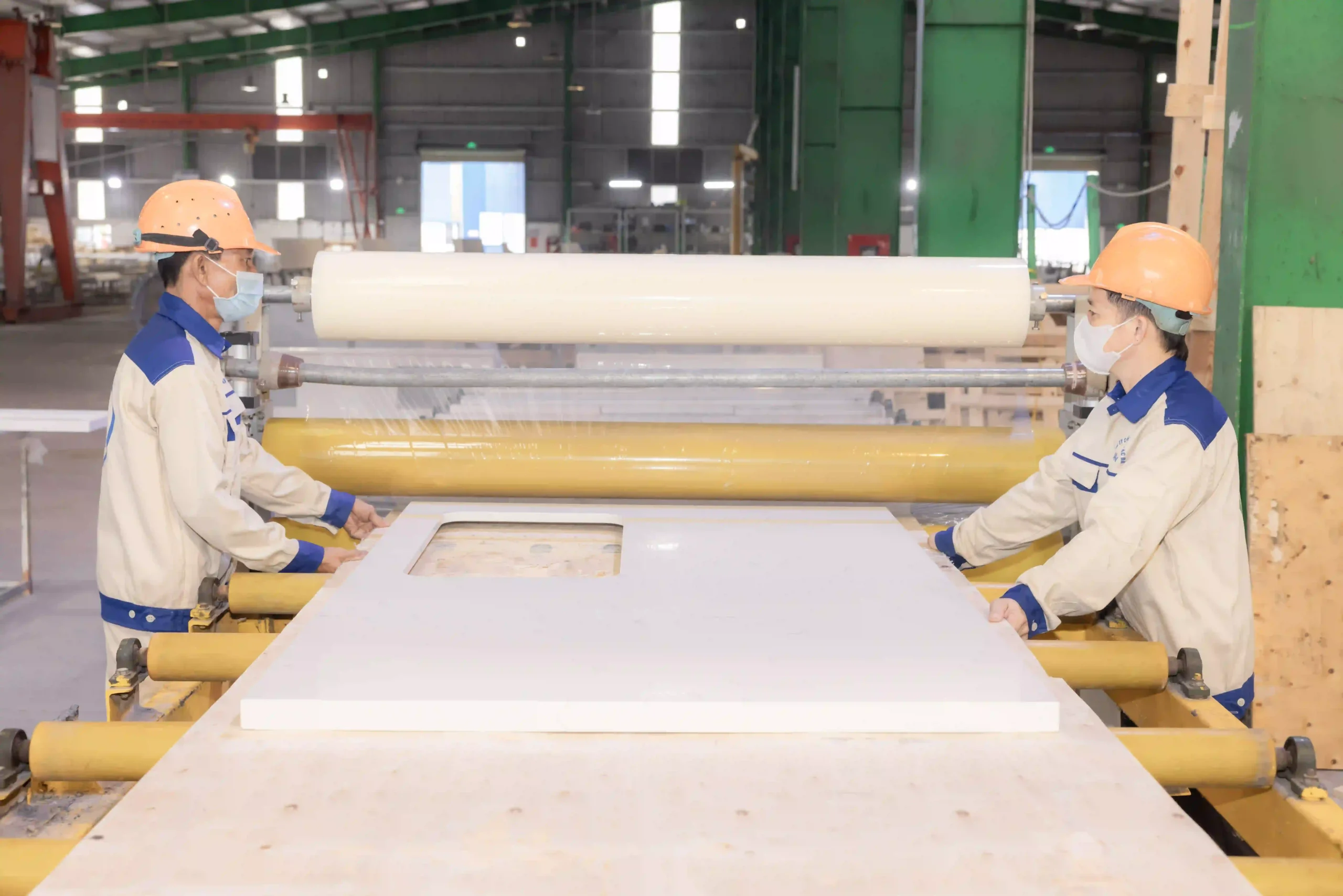
The Quartz Fabrication process at Dragon Quartz follows a carefully structured series of steps, ensuring that each product is manufactured to the highest quality.
1. Material Preparation
- Selecting slabs: Quartz slabs are sourced from reliable suppliers, ensuring the right color, size, and quality for each specific project.
- Quality inspection: Each slab is thoroughly inspected for cracks, voids, or other defects before being processed.
2. Measuring and Cutting
- Precise measurement: Based on technical drawings and client specifications, precise measurements are taken to ensure accuracy.
- Cutting the slab: CNC machines and automated bridge saws are used to ensure clean, precise cuts with minimal material waste.
3. Edge Shaping
- Edge profiling: Edges like beveled, rounded, or square are shaped using specialized grinding machines.
- Edge smoothing: Once shaped, the edges are smoothed and polished to ensure safety and a seamless finish.
4. Surface Finishing
- Polishing: The surface is polished to achieve a flawless shine using diamond polishing tools.
- Custom finishes: Surfaces can be finished in gloss, matte, or textured, depending on design preferences.
5. Drilling and Grooving
- Drilling: Holes for sinks or fixtures are drilled with precision, ensuring safe installation.
- Grooving: If required, grooves or special design elements are added to enhance functionality or aesthetic appeal.
6. Edge Sealing
- Adhesive selection: High-quality adhesive is used to bond edges with strong adhesion.
- Sealing the edges: Edges are bonded securely, and excess adhesive is removed for a smooth, polished finish.
7. Cleaning and Final Inspection
- Cleaning: After fabrication, each product is thoroughly cleaned to remove any dust or debris.
- Final quality check: A detailed inspection is performed to check the product’s gloss, edge quality, and dimensions.
8. Packaging and Shipping
- Packaging: Each product is carefully packed using protective materials to ensure safe transportation. For more information about shipping details, please contact us!!
3. Quality Control at Dragon Quartz
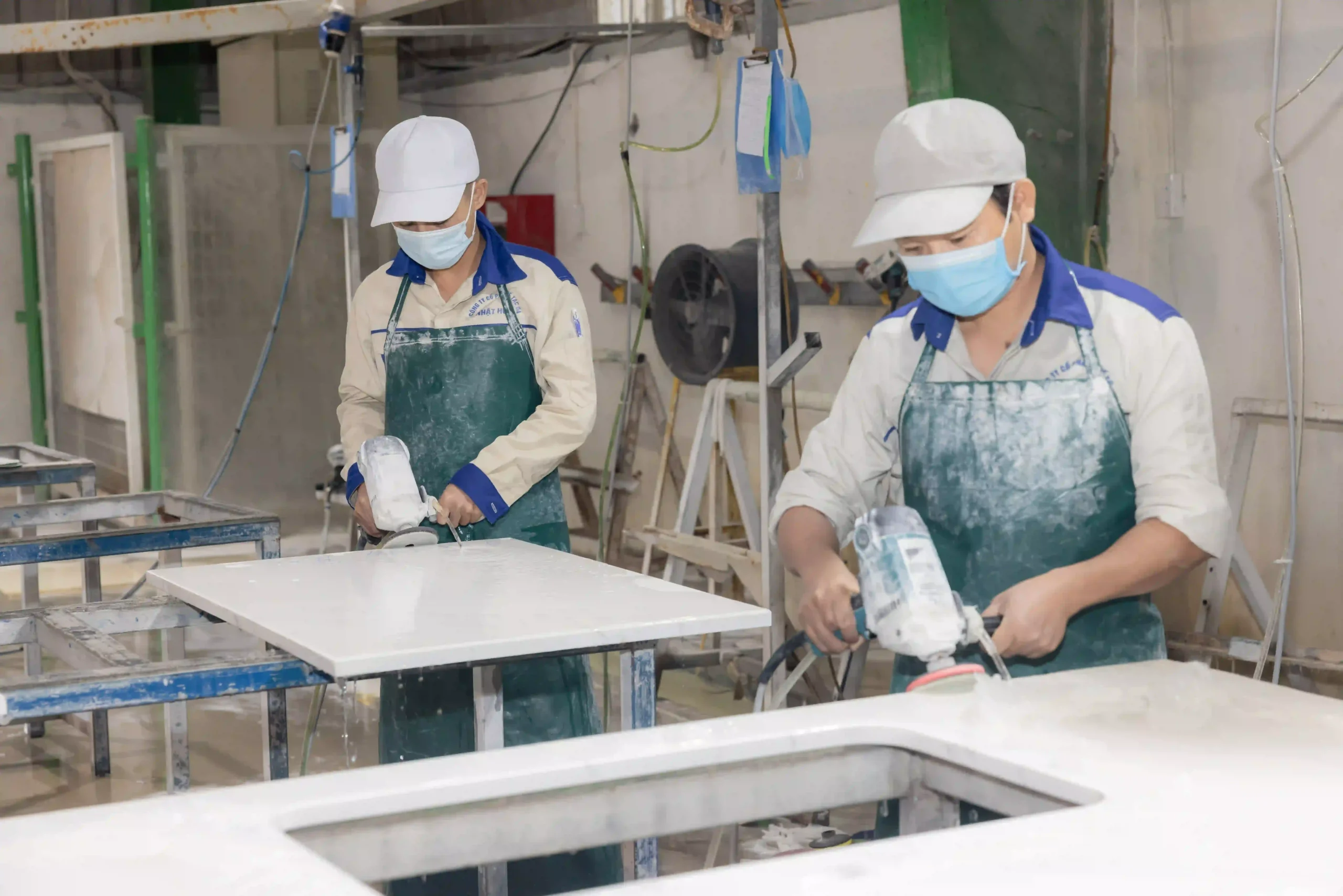
Dragon Quartz applies a rigorous quality control process to ensure that every product meets international standards. Our quality assurance team is involved at every stage of production, from initial material inspection to final product checks.
- Incoming inspection: Each slab undergoes careful inspection for defects like cracks or voids.
- Production monitoring: Every step in the production process is monitored to ensure compliance with thickness, dimension, and finish specifications.
- Final product inspection: Products are assessed for color consistency, surface gloss, and exact measurements before being approved.
- Pre-shipment inspection: Each batch of products is inspected again to ensure uniform quality and secure packaging.
4. NHG Factory: Advanced Technology and Skilled Workforce
At the heart of Dragon Quartz’s success is our NHG Factory, a state-of-the-art facility equipped with the latest machinery and technology. The factory combines cutting-edge equipment with a skilled workforce to deliver top-tier quartz products that meet the highest international standards.
Advanced Machinery for Precision and Efficiency
Our factory is equipped with high-precision CNC machines, automated cutting bridges, and diamond polishing tools, ensuring that each quartz slab is cut, shaped, and finished with accuracy and consistency. This advanced technology reduces material waste and guarantees that each product is crafted to perfection.
- CNC Machines: Enable precise, detailed cuts and customization for intricate designs.
- Automated cutting and polishing equipment: Ensures flawless cuts and a smooth, polished surface.
- High-tech polishing machines: Deliver a durable, high-gloss finish, or custom finishes such as matte or textured, based on client needs.
Skilled Workforce Ensuring Quality Craftsmanship
While advanced machinery is crucial, Dragon Quartz also prides itself on its team of highly skilled professionals. Our workers are experts in operating the technology and applying their craftsmanship to deliver perfect results.
- Expert Technicians: Operate advanced machinery to ensure precision in every cut and finish.
- Craftsmen: Apply their skills to refine complex edges and designs, ensuring each product’s perfection.
- Quality Control Specialists: Oversee the entire production process, ensuring each slab meets our stringent quality standards before it leaves the factory.
Continuous Training and Development
To stay at the forefront of the industry, Dragon Quartz invests in ongoing training and development for our workforce. This allows our team to remain up-to-date with the latest fabrication techniques and trends, ensuring we continue to meet the demands of modern interior design.
5. Why Choose Dragon Quartz?
Choosing Dragon Quartz means choosing unparalleled quality, flexibility, and innovation in quartz fabrication. We offer several advantages that set us apart from the competition:
1. Guaranteed Quality
Each product is carefully inspected throughout every stage of the fabrication process, ensuring it meets the highest standards for both durability and beauty.
2. Domestic Production
With a factory located in Vietnam, Dragon Quartz can offer faster delivery times and lower shipping costs, all while maintaining excellent customer service and warranty support.
3. Advanced Technology
By utilizing cutting-edge machinery and a fully integrated production process, we can meet custom design requests with high precision and efficiency.
6. Conclusion
Dragon Quartz is a trusted partner for high-end interior projects, with our professional Quartz Fabrication process and rigorous quality control measures. Our modern NHG Factory, combined with a team of skilled experts, ensures that each quartz product meets international standards in terms of quality and aesthetics. Moreover, we also have printed quartz technology, one of the optimal solutions for your space Let Dragon Quartz turn your design ideas into reality with unmatched craftsmanship and timeless elegance.
Contact us today to learn more about Dragon Quartz’s services and products!